Be on the safe side when it comes to calibrating gas sensors for gas detection.
WHY is calibration of gas sensors important?
Gas sensors from MSR-Electronic are used in a wide range of applications, such as in laboratories and medicine, garages and tunnels, aquaculture systems, shipping, etc. To improve the service life and precision of the sensors, it is necessary to calibrate and adjust the sensors regularly. This is the only way to ensure that the measurements are accurate, reliable and reproducible. The calibration and adjustment process is used to identify and correct deviations.
WHAT advantages does calibration offer?
- Accuracy of the measurements: Regular calibration ensures that the gas sensors provide accurate readings. This is particularly important in environments where accurate measurements are crucial for the safety of people, the environment and systems
- Long-term stability: Calibration helps to detect changes in sensor performance and correct them if necessary. Long-term stability is important to ensure that the sensors provide reliable readings even after extended use.
- Compliance with regulations and standards: Many industries have regulations and standards that require accurate measurements of gases. Calibration ensures that the sensors meet these requirements and comply with legal regulations.
- Error detection: Calibration also serves to detect faults in the gas sensor at an early stage. This allows maintenance or repair measures to be taken in good time to avoid failures or inaccurate measurements.
The time line for calibration are explained in the data sheets. The complete calibration process is described in detail in the videos and the instructions for use. In addition to the recommendations on calibration intervals, there are also legal regulations that specify the interval, depending on the application and region. The following graphic illustrates the longer service life of the sensors as a result of calibration:
HOW is calibration carried out?
Calibration ensures that the sensors provide accurate measurements. There are various methods for calibrating gas sensors, depending on the type of sensor and the requirements of the application. The basic procedure is as follows:
- Preparation: Ensure that the sensor is correctly installed and ready for operation. Also check that all the necessary tools are available. It is also important that the environment is free of gases that could affect the calibration. Ideally, the room should be ventilated to ensure even air distribution.
- Zero calibration: Zero calibration is carried out to ensure that the sensor provides stable values in the absence of the gas to be measured. To do this, the sensor is placed in a clean air environment in which the gas to be measured is not present. The sensor is then adjusted to the zero point to ensure that no incorrect values are displayed.
- Interference correction: In some cases, other gases or environmental conditions may affect the accuracy of the measurement. In such cases, additional calibration steps may be required to compensate for these interferences and ensure accurate measurements.
- Checking and documentation: After calibration, the results should be regularly checked for functionality and performance and documented. This includes recording the calibration steps performed, the measured values and other relevant information.
It should be noted that the exact steps and methods for calibrating gas sensors may vary depending on the sensor type, manufacturer's instructions and specific requirements. You will be guided through the entire calibration process by means of simple menu navigation. Calibration of the MSR sensors is equivalent to adjustment. It is recommended that you follow the sensor manufacturer's instructions exactly and seek professional support if necessary.
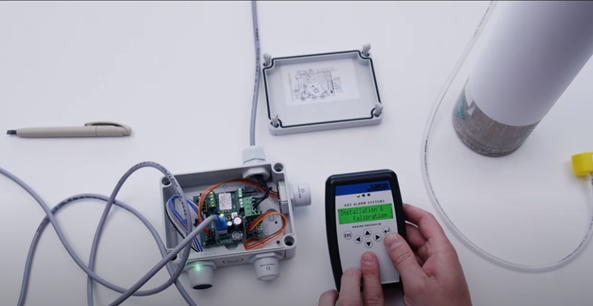
WHAT must be considered for recalibration?
When recalibrating, it is important to know the sensor type, gas type and measuring ranges of the sensors. It should also be clarified in advance whether the sensors are individual detectors or whether they are connected to a controller. Data sheets and operating instructions specify which tools are required.
MSR Electronic offers a hand tool (STL06) and software (PCE06) with adapter cable for this purpose and recommends using a gas in the range of 30% to 90% for calibration and a gas in the range of 50% of the measuring range for semiconductor sensors. You will need zero gas and test gas, a gas regulator and the corresponding sensor adapter. The gas flow rate and gas exposure time can be found in the table in the sensor user manual. It is also important to take into account the warm-up time of the sensor. You can find out more about the recalibration process here. The MSR-Electronic support team is also available to answer technical questions.
WHICH tools can be used for calibration?
MSR-Electronic recommends using the following tools for sensor calibration:
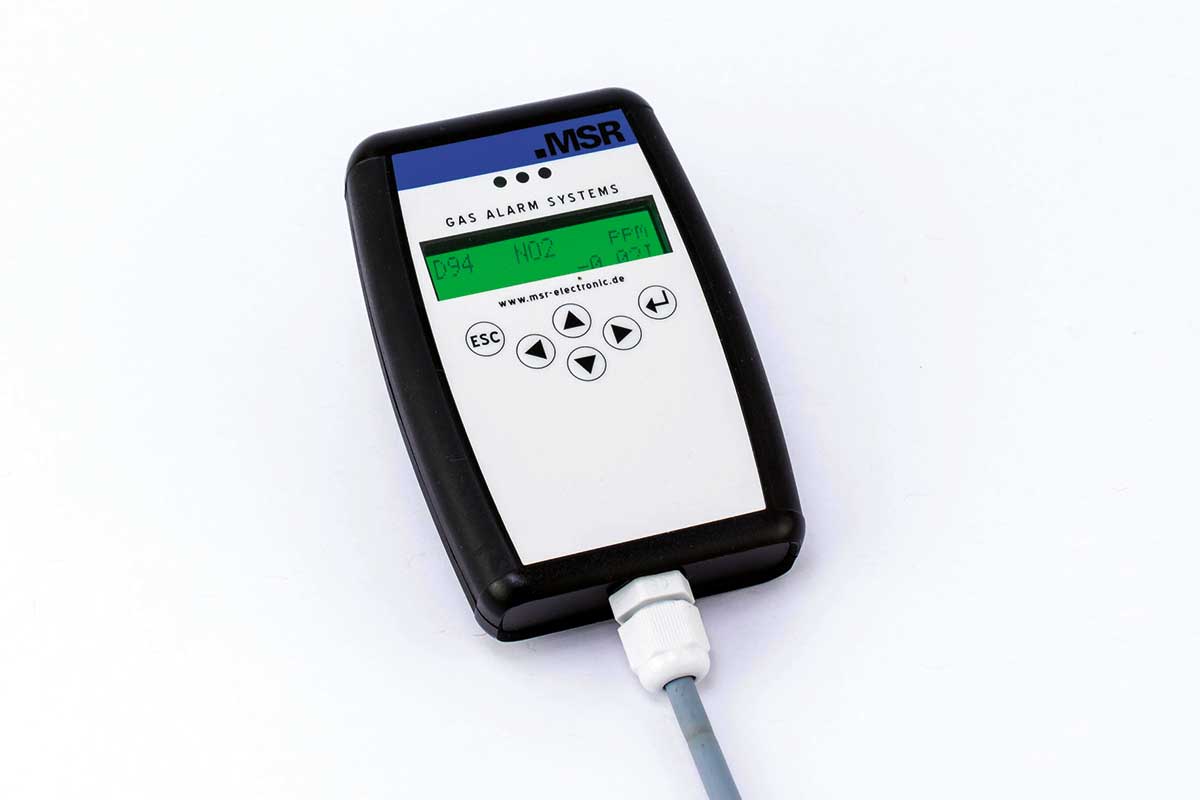
STL06
The STL06 service tool is a stand-alone, menu-driven tool for addressing, parameterizing and calibrating the devices for the PolyGard® and PolyXeta® product series. Communication and power supply are provided via a cable that is plugged into the respective devices.
Click here for the how-to video "Calibration with the STL06 tool"
PCE06
The PCE06 software with associated hardware is a tool for addressing, parameterizing and calibrating the devices for the PolyGard® and PolyXeta® product series. Communication with the PC and power supply to the tool is via the existing USB interface. Communication with the devices is via a cable with a suitable connector.
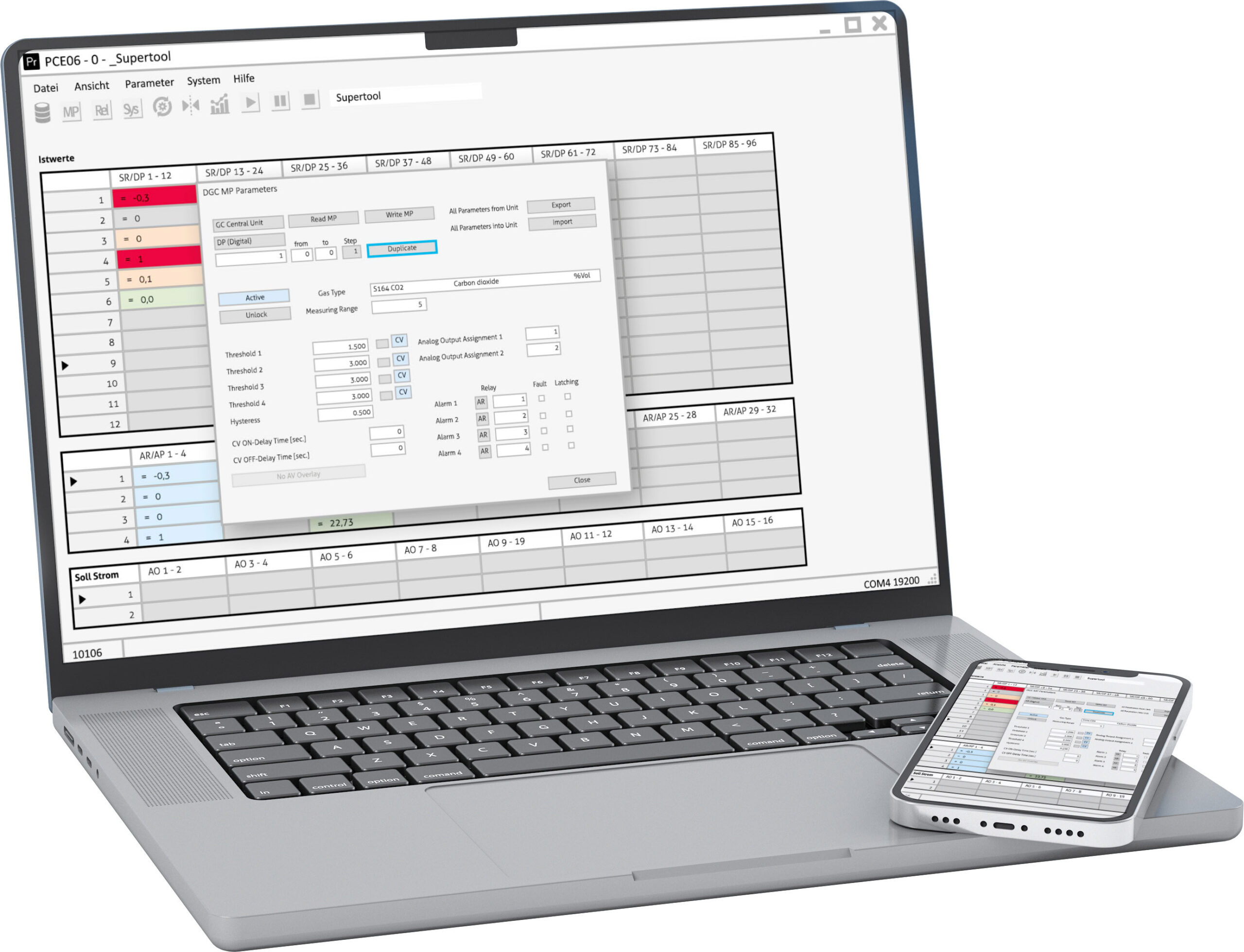
When you choose a gas detector from MSR-Electronic, you benefit from many advantages such as quality, availability, competitive products, responsibility to clients and business partners and openness to individual requirements. Calibrating the sensors regularly will ensure their high level of quality and performance in the long run.
Further information on MSR products can be found in the current online catalog or in the webshop www.msr-24.com.