Gas sensors from MSR-Electronic monitor individual production steps in ATEX zone 1 and 2
Who doesn’t know it – the much-used polystyrene, popularly known as Styrofoam – it serves:
- for insulating buildings
- to save a lot of CO2
- for protecting people, goods and food, e.g. crash helmets, packaging for televisions and fresh products
The special advantage of polystyrene:
- It is extremely light.
- Against heat and cold it insulates excellently .
- It is very resistant to mechanical and chemical influences.
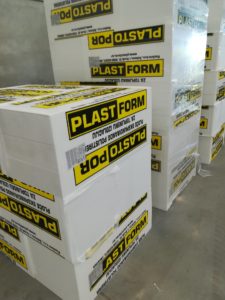
©Plastform d.o.o.
Production of polystyrene
Petroleum is needed for the production of polystyrene. In classic suspension polymerisation, water and styrene are mixed. With the addition of the blowing agent pentane, the mixture forms a bead-shaped granulate, the expandable polystyrene (EPS).
As soon as the EPS beads are heated with steam, they inflate to about fifty times their original size.
After intermediate storage, the foam beads are filled into block moulds and welded together by heating them again with steam.
The resulting polystyrene blocks are cut into sheets after a certain storage time.
Plastform d.o.o. in Croatia specialises in the production of polystyrene for use as thermal insulation in the construction industry and for the production of polystyrene packaging for use in industry and agriculture.
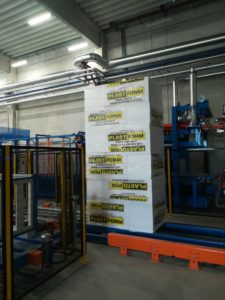
©Plastform d.o.o.
Monitoring the concentration of pentane gas with gas sensors from MSR-Electronic
Gas sensors from MSR-Electronic monitor the concentration of pentane gases in the individual production steps to prevent the formation of explosive mixtures.
Plastform’s production plant relies on the reliable gas measurement of the PolyXeta®2 product series from MSR. As a result, gas monitoring takes place in Ex Zone 1 when protecting polystyrene (EPS) in the vapour-permeable silos.
Furthermore, explosive pentane gas is detected in Ex zone 2 during the storage of raw materials and in the ingot casting process. The fixed gas warning system switches on the ventilation at a measured concentration of 10 % LEL.
If this is not sufficient and the concentration has reached 20 % LEL, the gas detection system interrupts the pentane supply and stops the production process.
Solutions from MSR-Electronic for gas measurement in ATEX Zone 1 and 2
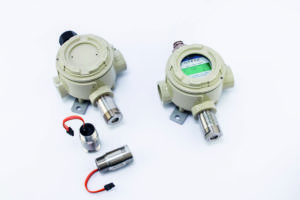
© MSR-Electronic GmbH, Germany, PolyXeta®2 gas sensor
The PolyXeta®2 sensor is used in:
- industrial areas such as the oil/gas industry
- biogas plants
- petrochemical plants
- power stations etc. in Ex zones 1 and 2
It is also suitable for commercial areas such as gas transfer stations.
The microprocessor-based gas sensor with 4–20 mA / RS-485 Modbus output signal, alarm and fault relay (all SIL2 certified) is used to monitor the ambient air to detect combustible gases and vapours by means of a catalytic sensor element (Pellistor) in accordance with Directive 2014/34/EU.
For sensors without LC display, calibration is done via a handy calibration device or the PC software. Sensors with LC display have an integrated calibration routine that is started from the outside with a permanent magnet without opening the housing.
In addition, the background lighting changes from green to red in the event of an alarm or error.
BENEFITS
- MSR-Electronic has ATEX and IECEx certificates for electrical explosion protection and metrological testing as well as SIL2 for the safety functions 4-20 mA, RS-485 and relay (pellistors only).
- 2 versions: with flameproof enclosure or ignition protection type
- Enclosure: additional FM and CSA certificate for Class I, Div. 1
- Continuous monitoring
- Microprocessor with 12-bit converter resolution
- Self-monitoring
- Easy calibration / calibration service by replacing the sensor head
- Proportional 4–20 mA output
- Serial interface to the control centre
- Reverse polarity and overload protected
Further information on MSR products can be found here in the current MSR-Electronic online catalog or in the webshop www.msr-24.com.
The entire support of the MSR gas warning system was carried out by the certified MSR partner Aurel d.o.o. directly on site.